Machine Hour Rate: Calculation, Advantages and Disadvantages!
Machine hour rate is the cost of running a machine per hour. It is one of the methods of absorbing factory expenses to production. It is used in those industries or departments where machinery is predominant and there is little or practically no manual labour. In such industries or departments, overhead consists of indirect expenses in running and operating the machine.
Therefore, it is desirable to allocate overhead to production on the basis of working hours of the machines. It is not desirable to calculate the machine hour rate for the entire factory but different rates may be calculated according to their make, type, size, capacity, wattage, horse power and other factors relating to each machine or group of machines as a cost centre.
Advantages And Disadvantages Of Manual Labor Originally most products were made on an individual as-needed basis; if a tool was required it was fashioned by hand and in turn used to make more tools. As time passed, more complex techniques were developed to help people accomplish fabrication and production tasks. Advantages Disadvantages It is simple and economical to apply. This method does not differentiate between skilled and unskilled labours. It gives importance to time factor for overhead absorption. The method does not recognise differences between manual and mechanical production. Labour rates are more stable than material prices. Less labour – human intervention is very minimal with CNC Milling. There is not as much skill and experience required to use the lathe and produce quality components. Uniformity – one of the greatest advantages of CNC milling machines is they can produce the same product over and over again. With CNC milling, the dimensions are similar in.
ADVERTISEMENTS:
Machine hour rate is obtained by dividing the total running expenses of a machine during a particular period by the number of hours the machine is estimated to work during that period.
Calculation of Machine Hour Rate:
The information required for calculation of machine hour rate is cost of the machine; cost of installation of the machine; scrap value, if any; life of the machine in hours; standing charges like rent etc. allocated to the machine; repairs and maintenance of the machine; power consumption; set up time; cost of lubricants applied on the machine and insurance premium of the machine, if any.
Following steps are required to be taken for the calculation of machine hour rate:
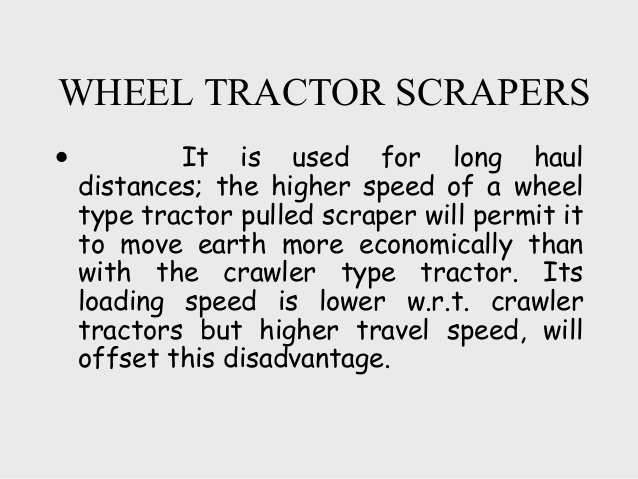
1. Each machine or a group of machines should be treated as a cost centre so that all overheads relating to that machine or machines may be identified.
2. Overheads relating to a machine are divided into two parts i.e., fixed or standing charges and variable or machine expenses. Standing charges are those expenses which remain constant irrespective of the use or running of machine and examples of such expenses are rent and rates, lighting and heating, insurance, supervising labour etc. Machine expenses as power, fuel, depreciation, repairs etc. vary with the use of the machine.
3. Standing charges are estimated for a period for every machine and amount so estimated is divided by the total number of normal working hours of the machine during that period in order to calculate an hourly rate for fixed charges. For machine expenses an hourly rate is calculated for each item of expenses separately by dividing the expenses by the normal working hours. While calculating the normal working hours, the hours which are required for maintenance or for setting- up or setting-off are to be deducted.
4. Total of standing charges rate and the machine expenses rate will give the ordinary machine hour rate. If machine operator’s wages are also added into the simple machine hour rate then it will be called comprehensive machine hour rate.
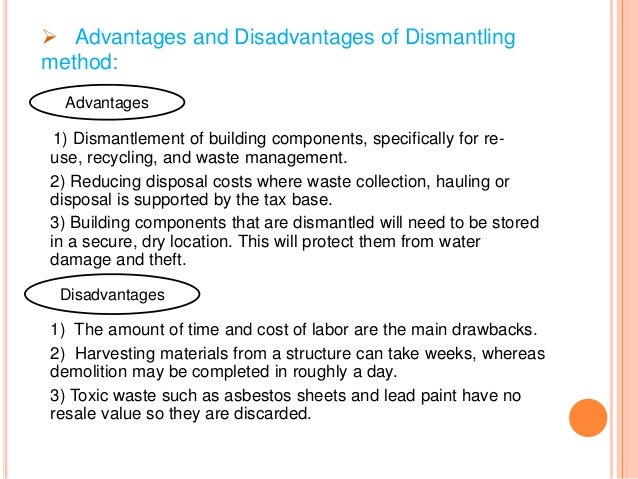
5. Sometimes supplementary rate is used when the charge for all other overhead cost is not included in the machine hour rate i.e., only machine expenses are taken for the purpose of machine hour rate. It is also used for correcting any error in the determination of machine hour rate due to which there is heavy over- or under-absorption of overheads.
ADVERTISEMENTS:
The bases which may be adopted for apportioning the different expenses for the purpose of calculation of machine hour rate are given below:
Advantages:
1. It helps to compare the relative efficiencies and cost of operating different machines.
2. It brings to light the existence and extent of idle time of machines.
3. It enables the management to decide how far the use of machine work is preferable to manual work.
4. It is most scientific, practical and accurate method of recovery of manufacturing overheads.
5. Cost reports prepared with the help of such rate are dependable and can help the management in decision-making.
ADVERTISEMENTS:
6. It provides useful data for estimating cost of production, setting standards and for fixing selling prices for quotations.
7. It provides ready method for measuring the cost of idle machines if separate rates for fixed and variable overhead rates are calculated. When hourly rate is fixed on the basis of anticipated running hours of the machine, there is under-absorption of fixed overhead expenses if actual running hours are less than the estimated.
Disadvantages:
1. It involves additional work in assessing the working hours of machines and thus it is a costly method.
2. It does not take into account expenses that are not proportional to the working hours of machines.
3. It gives inaccurate results if manual labour is equally important.
4. It is difficult to estimate the machine hours especially when production programme is not available in advance.
5. Blanket rate cannot be used and it makes the method more costly.
Illustration 14:
ADVERTISEMENTS:
A machine is purchased for cash at Rs 9,200. Its working life is estimated to be 18,000 hours after which its scrap value is estimated at Rs 200.
It is assumed from past experience that:
Illustration 18:
A manufacturing company uses two identical large and four identical small machines. Each large machine occupies one quarter of the workshop and fully employs three workers; each small machine occupies half the space of a large machine and fully employs two workers. The workers are paid by piece work.
Each of the six machines is estimated to work 1,440 hours per year, while the effective working life is taken as 12,000 working hours for each large machine and 9,000 working hours for each small machine. Large machines cost Rs 20,000 each, and small machines Rs 4,000 each. Scrap values are Rs 4,000 and Rs 100 respectively.
Repairs, maintenance and oil are estimated to cost for each large machine Rs 4,000 and for each small machine Rs 1,200 during its effective life.
Power consumption costs 5 P. per unit and amounts for a large machine 20 unit per hour and Tor a small machine 2 unit per hour.
The manager is paid Rs 4,800 a year and workshop supervision occupies of his time, which is divided equally among the six machines.
Details of other expenses are:
Rent and rates for workshop Rs 6,400 a year, Lighting (to be apportioned in the ratio of workers employed) Rs 1,820 a year.
Taking a period of three months as a basic, calculate the Machine Hour Rate for a large machine and a small machine respectively.
ADVERTISEMENTS:
Solution:
Computation of Machine Hour Rate:
Set-up Time:
In the factories it is absolutely normal that some time is lost or consumed on the frequent setting up the machines. The loss of time may be because of changes from one job to another or because of breakdown etc. This time means the time when the machine is just idle. This is called making machines ready time.
The cost of all such hours lost in setting up of the machines (including wages of workers as well as other overheads) may be spread over the jobs actually completed. Sometimes even separate machine hour rate are computed for running (productive) and this set up (unproductive) time. Through this method one can ensure the full absorption of the manufacturing overheads.
Illustration 19:
A manufacturing unit has purchased and installed a new machine of Rs 12, 70,000 to its fleet of 7 existing machines. The machine has an estimated life of 12 years and it is expected to realize Rs 70,000 as scrap at the end of its working life.
Other relevant data are as follows:
(i) Budgeted working hours are 2,592 based on 8 hours per day for 324 days. This includes 300 hours for plant maintenance and 92 hours for setting up of plant.
(ii) Estimated cost of maintenance of the machine is Rs 25,000 (p.a.)
ADVERTISEMENTS:
(iii) The machine requires a special chemical solution, which is replaced at the end of each week (6 days in a week) at a cost of Rs 400 each time.
(iv) Four operators control operation of 8 machines and the average wages per person amount to Rs 420 for week plus 15% fringe benefits.
(v) Electricity used by the machine during the production is 16 units per hour at a cost of Rs 3 per unit. No current is taken during maintenance and setting up.
(vi) Departmental and general works overhead allocated to the operation during last year was Rs 50,000. During the current year it is estimated to increase 10% of this amount.
Calculate machine hour rate, if (a) setting up time is unproductive; (b) setting up time is productive.
Rate per Unit of Production:
This method is simple, direct and easy. It is suitable for mining and other extractive industries, foundries, brick laying industries, where the output is measured in convenient physical units like number, weight, volume etc.
The rate is calculated as under:
For example, if the overhead expenses (budgeted) are Rs 60,000 and budgeted production is 10,000 tonnes then overhead rate according to this method will be Rs 6 per tonne.
The main limitation of this method is that it is restricted to those concerns which produce only one item of product or a few sizes, qualities or grades of the same product. If more than one item is produced then it is essential to express dissimilar units against a common denominator on weightage or point basis.
Sale Price Method:
Under this method budgeted overhead expenses are divided by the sale price of units of production in order to calculate the overhead recovery rate.
The formula is:
The method is more suitable for apportioning of administration, selling and distribution, research, development and design costs to costs of products. It can also be used with advantage for the preparation of joint products costs.
This method is arbitrary and recovery made by this method is inequitable because overhead costs have practically no relationship with the sale price of the products.
Overhead Rates for Service Cost Centres:
Generally overhead rates are fixed for production cost centres. Service departments’ costs are apportioned to production departments on equitable basis.
Sometimes, under the following circumstances, separate overhead rates are determined for service departments:
(i) When the base adopted for the recovery of production overhead is not suitable for service departments.
Advantages And Disadvantages Of Manual Labour In Economics
(ii) When a service department is partly producing and partly rendering services to other departments.
Advantages And Disadvantages Of Manual Labour Theory
A separate rate for material storage and handling costs is fixed. Similar rates may be fixed for the Tool Room, Inspection and Packing Department.
Choice of an Overhead Rate:
The method adopted for overhead absorption varies from industry to industry and from one undertaking to another. Some firms use separate overhead rates for each type after classifying the overhead expenses into several types. The choice of a most equitable method is very important as the method adopted, if unsuitable, will distort costs and will be useless for control and decision-making purposes.
Type of industry, nature of products and process of manufacture, organisation set up, individual requirements and policy of management are the factors which affect the choice of an overhead rate. Besides these, a satisfactory overhead rate should be simple, easy to operate, practical, accurate, economic in application, fairly stable and related to time factor. It should be preferably departmental rates as compared to blanket rates, homogeneous cost unit and should lay stress on the main production element of the concern.
Following factors should be taken into consideration before formulating overhead rates or deciding upon the basis for applying overheads to products:
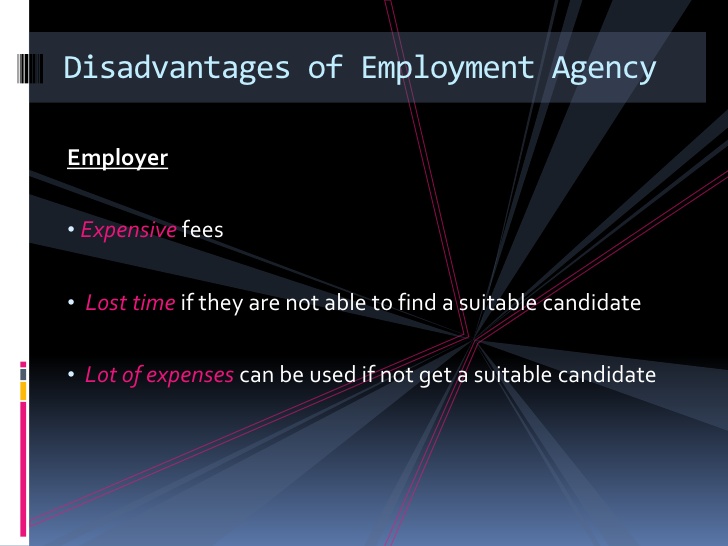
1. Equitable apportionment of overhead:
The overhead rate should be such that overhead should be equitably apportioned to the cost centres or cost units. The amount of overheads recovered should also be equivalent to the amount of overheads incurred.
2. Simple and easy to understand:
The overhead rate should be simple to calculate and easy to understand. It should be convenient in application. It should not require unnecessary or additional clerical work.
3. Relation with time factor:
Overhead rate should have some relation to the time taken by various jobs for completion. Thus, if a job takes twice as much time as another job, the first job should be charged twice the amount charged to the second job. It is because of this reason that direct wages percentage rate is preferred over direct material cost percentage rate.
4. Separate rates for manual or machine work:
The work done by manual labour should be distinguished from work done by machines and different overhead rates should be applied for manual and machine work. For example, when work is done by manual labour, it should not be charged for anything in respect of machine expenses like depreciation, repairs, maintenance etc.
5. Different overhead rates for different departments:
Different overhead rates should be ascertained for different departments where the nature of the work done by one department is different from the work done by other department or departments.
6. Selection on availability of information:
The selection of most appropriate overhead rate depends on the extent of information available or recorded. For example, labour hour rate can only be applied where labour time cards are maintained to record time spent by workers on each job, process or product.
7. Change of method:
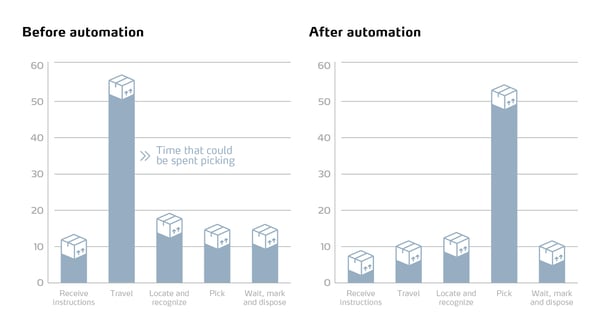
The method should be subject to change from time to time depending upon the changes in the factors on which it is based.
8. The work done by skilled workers should be distinguished from work done by unskilled workers:
Normally unskilled workers do more wastage of materials, more wear and tear of machinery and greater supervision on them is required because they are not skilled in doing the work. Hence, method of absorption should make distinction between work done by skilled workers and that by unskilled workers because work done by unskilled workers should have correspondingly higher proportion of factory expenses. As a matter of fact, separate rate should be calculated for each category of workers.